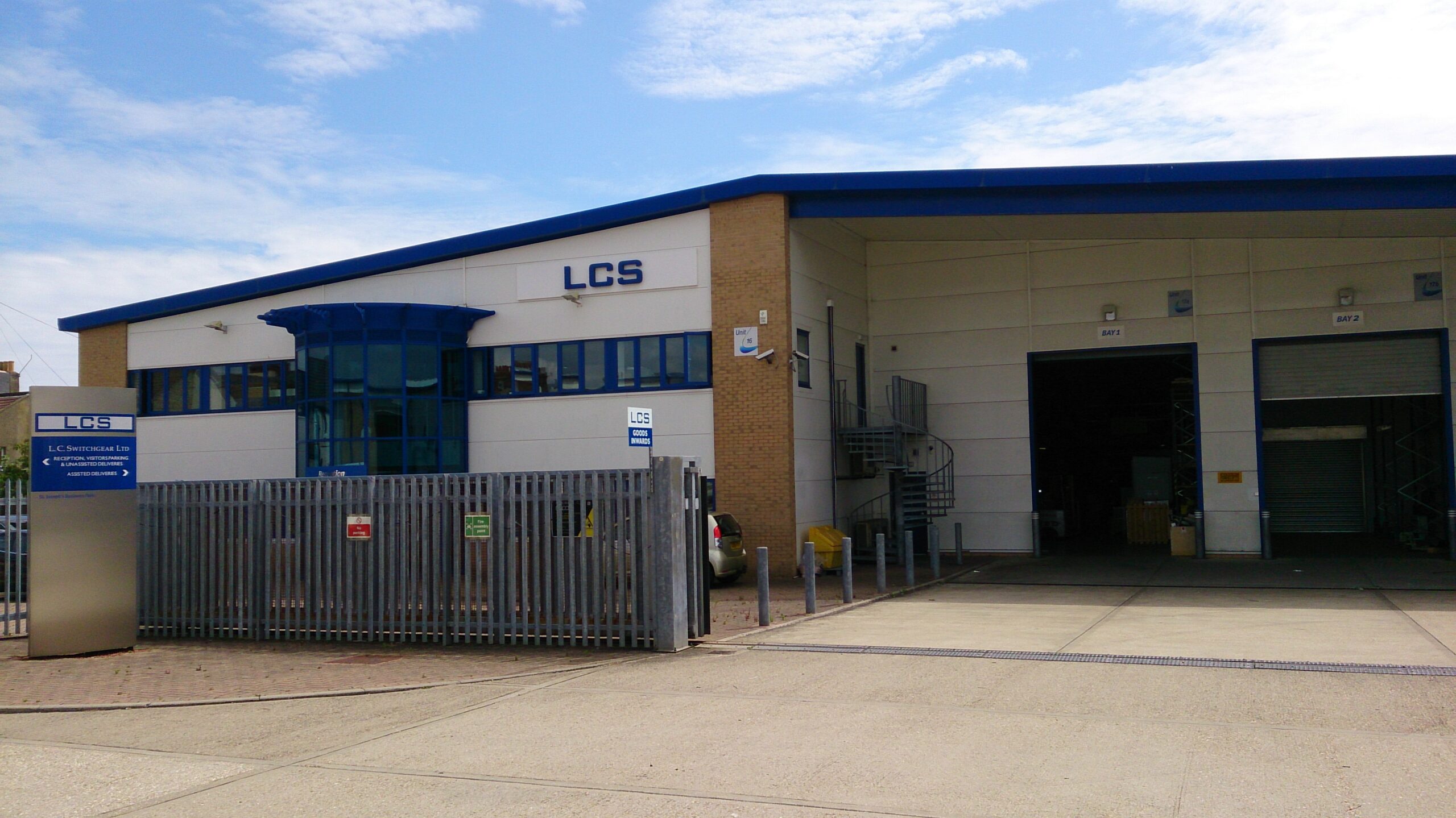
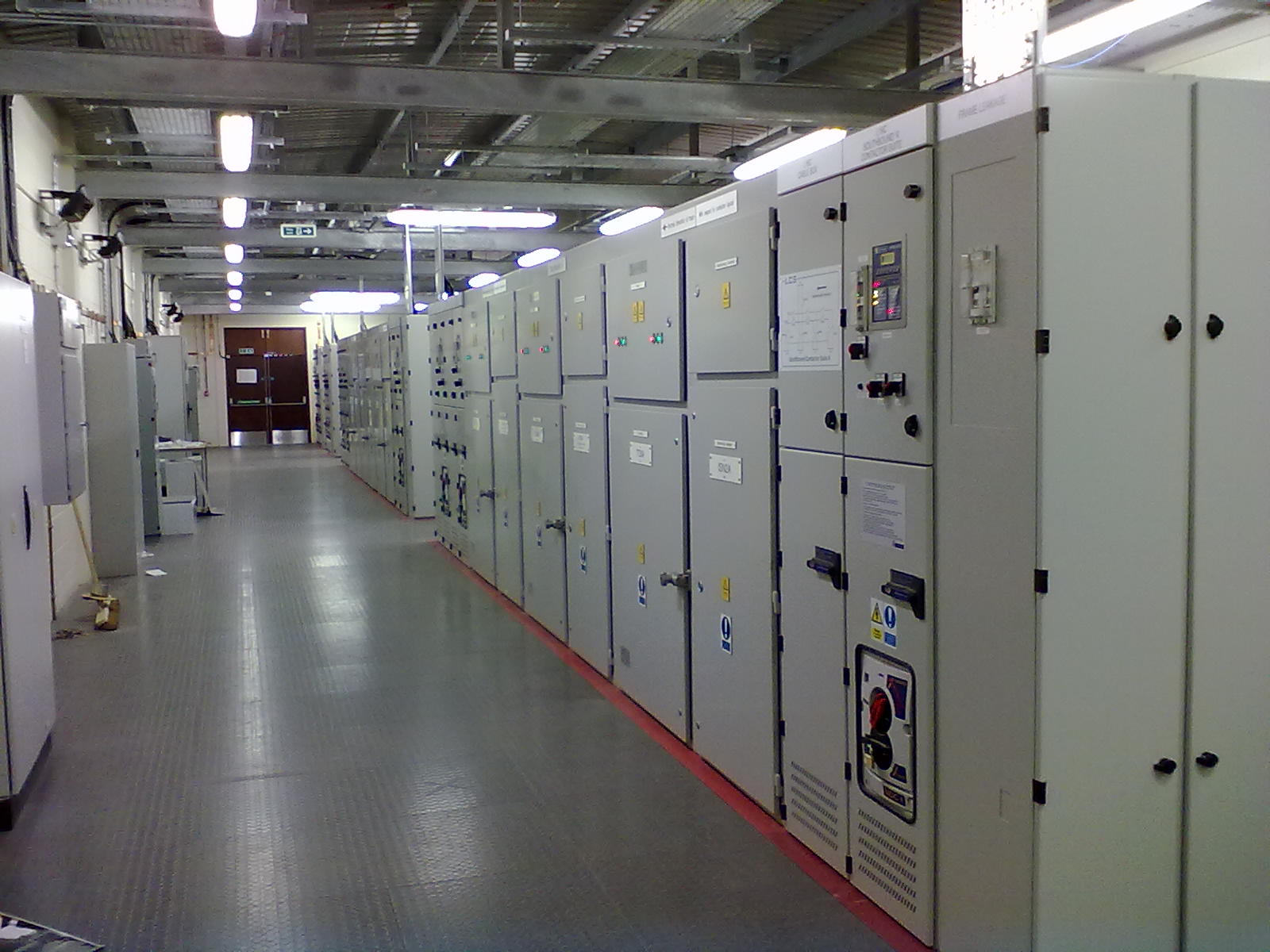
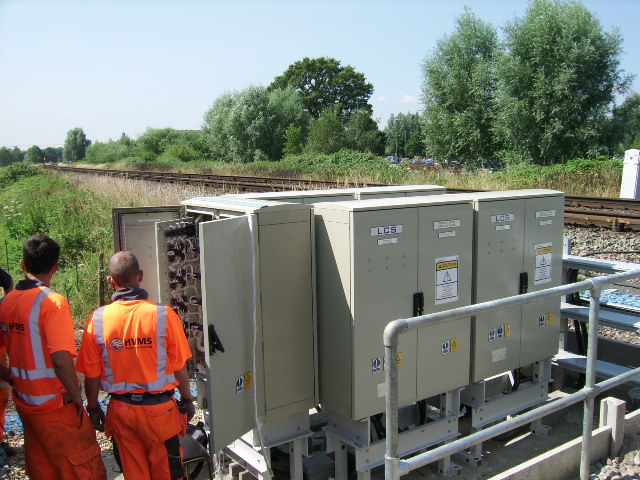
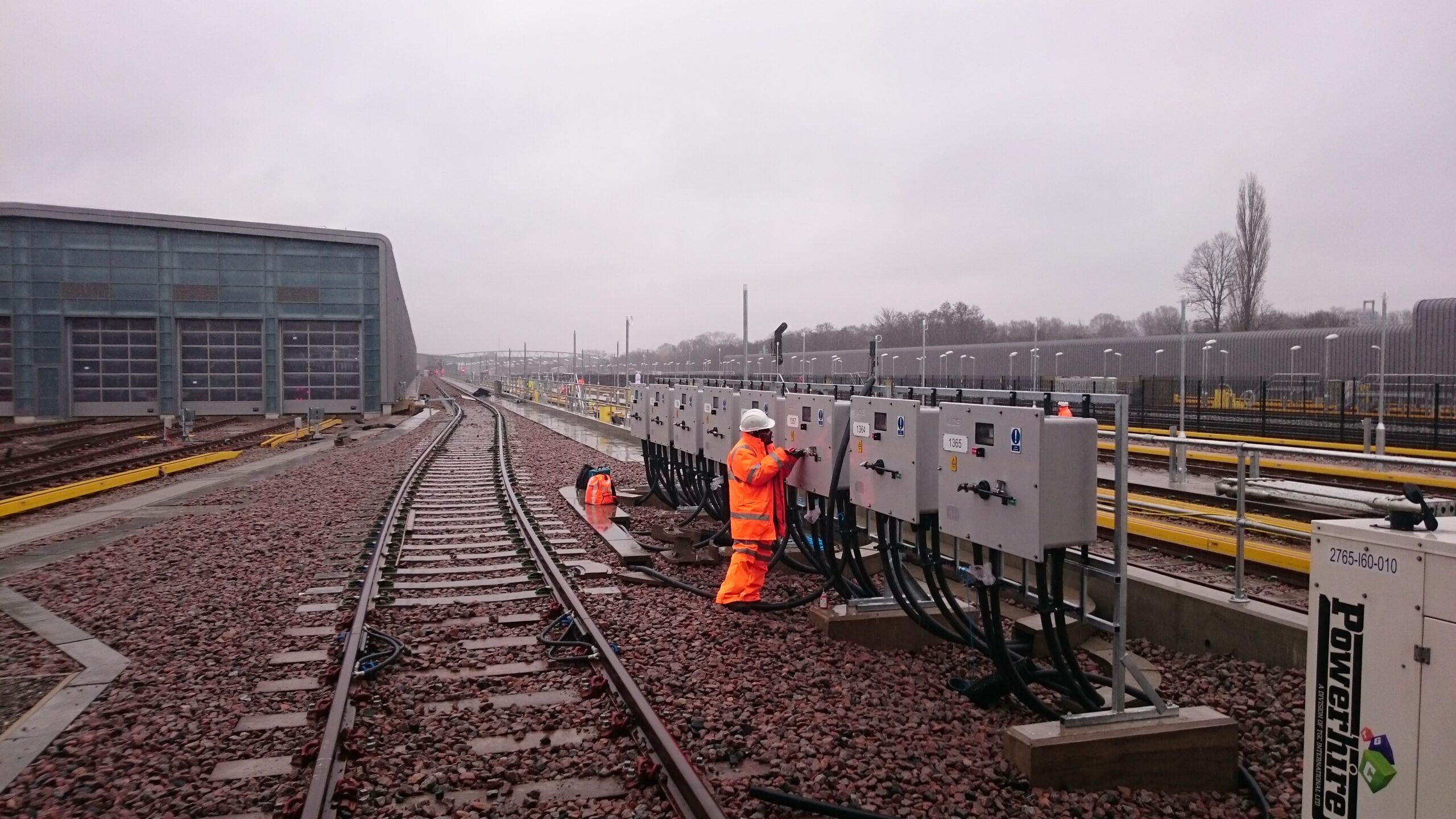
Design
LCS have a highly experienced and skilled design team. We follow stage gated design processes based on PMBOK and Design for Reliability to ensure a robust design. We have an extensive product portfolio however, if you require a none standard product, we can offer either variations to the existing range or completely bespoke offers.
Manufacturing
All assembly work is carried out at our specialist facilities in Hove, covering both the AC and DC sides of our business. We are known for our care and attention to the build process, ensuring that the product is manufactured to the highest standards.
Testing
As well as carrying out routine testing on all our products before they leave the factory, we can also carry out development and type testing in house. We have links with external test facilities for more advanced requirements. Testing can range from a single component to a complete suite of panels.
Maintenance
LCS offer a full range of support services to compliment and augment our product offerings. Whilst our product range consists of equipment which requires little maintenance, regular servicing will extend the life of your products. An LCS service package could save you significant costs over the life of your system. We pride ourselves on a quick efficient service and endeavour to return products as quickly as we can.
Investigation
Experts in the fields of both DC & AC switchgear, LCS can investigate and analyse issues facing our customers. Investigations can take place at the customer’s premises, or if that is not feasible at our facilities in Hove. Comprehensive technical reports with clear recommendations are provided.
Installation
LCS offer expert installation services for our ac equipment. We specialise in installations in the most difficult of areas. Please see our time lapse videos as examples of our capabilities.
Customer: Network Rail
The PLC system has been developed to comply with the Network Rail operations diagram that detailed four suites. The specific requirements are given in N244 Procurement Specification 22. Ludgate Cellars Contactor Control system Functional Requirements version 2.0 The key requirements are
- That each suite has a PLC.
- That if as a result of a PLC failure it shall be possible to changeover to off line and standby suite shall continue normal operation.
- The control of each track Northbound and Southbound shall be fully independent.
- The system be 100% redundancy referred to as bomb proof or as near as possible.
- Each suite shall have a local display and shall be capable of indicating the status of the contactor suite in the other half of the substation.
This uses a total of 4 PLCs. Two for each direction of traffic. (A and B section of the substation) Each PLC has its own HMI (screen), inputs and outputs. Each pair of PLCs is connected using the various data cables shown. These are fibre optic in some cases which reduce the risk of interference or noise from unclean earth connections. The main interconnecting optic cables are routed differently within the substation to minimise the risk of damage to both. Each pair of PLCs is synchronized so that they act as one master and standby and give full redundancy in the event of a single failure. This gives the ability for them to change from master to standby very quickly. The PLC takes track circuit signals to determine which circuit is made and communicate with the SCADA system which controls the main power devices in the system.
Enclosure
- Steel enclosure painted RAL 7035 grey
- Environmental rating IP54
- Cable entry arranged through the top
Features
- Master / hot stand-by PLC
- 19″ colour touch screen
- Digital input and output modules
- SCADA interface
- SCADA controlled latching relay
- 48V to 24V DC – DC power supply
Customer: Network Rail
The Direct Current (DC) power supply was upgraded in 2005 for the introduction of the modern rolling stock and again in 2011 for the introduction of 12-car services. The DC traction power supply still operates below an N-1 capability in many places and the strategy in CP5 will be to bring the power supply network to an N-1 position that will give room for service growth and maintenance switch-outs without disrupting the timetabled services. It will be important that the whole system is upgraded where necessary to include the high voltage supply and equipment, the DC supply and associated equipment and the negative return bonding. The CP5 investment will be focused on DC switchgear renewal and electric traction equipment (ETE).
L.C. Switchgear are supplying Controlled Track Switches (CTS) and Negative Short Circuiting Devices (NSCD) for CP5. The CTS’s are used for quick on load DC isolation of the supplies while the NSCD’s are used to bond the conductor rails to enable quick SAFE access for maintenance and improvement in overnight possessions. This Smart Isolation is designed to give a longer working envelope in a possession and reducing the cost and duration of maintenance and moving toward a more efficient railway network.
The Controlled Track Switch (CTS) products are the same products used on CP4 and previously on the 2005 Power Supply Upgrade and the Channel Tunnel Reinforcement projects. These Controlled Track Switches (CTS), have been in service for many years. These units are Network Rail Accepted products; refer to Railway Products details. Electrification
The NSCD’s are a new product which combines two existing NR approved devices the LCS2 and the Bonding device associated with Depot CTS’s into one compact system.
The new Williams Way Substation has be built to supply the new Three Bridges depot. 4kA Bonding devices supplied by LCS are on the outgoing feeds to the depot which can be used to bond the outgoing supplies for maintenance.
LCS2 Disconnectors and alternative feed interlocked LCS2 Disconnectors are used to configure and isolate the various depot supplies to minimise disruption during routine maintenance. LCS Marshalling Panels collate the microswitch indication from the LCS2 to interlock with the appropriate Supply Circuit breakers.
The Three Bridges depot, which is split into east and west-side facilities either side of the London to Brighton mainline this comprises:
5 road, 12-car, maintenance building with the road supplies provided by LCS contactor panels specifically configured for this site. LCS Emergency stop panels marshal all of the emergency buttons from these roads.
11 train stabling and servicing roads, LCS Emergency stop panels marshal all of the emergency buttons from these roads. These signals are then grouped with equivalent signal from other sections of the depot in a master Emergency Stop Panel
There are 2 two carriage washing machines have DC electrical supplies fed through Wash Road Panels ensuring that the Washing machines are operated with the DC supply isolated and the tracks bonded.