Thick Film Technology
Ferro Techniek are masters of Thick Film Technology, and we have been at the forefront of its development for most of our history.
With extensive experience and a large portfolio of exclusive innovations, you can be confident that your requirements can be fulfilled with our thick film technology.
Below you will find a technical overview of Thick Film, as well as information on some of our more advanced techniques.
Layers
Tracks
Shapes
Assemblies
EFAST
Sensing
Element Layers
The base of a Thick Film element is typically a stainless steel substrate. This substrate is enamelled with a glass-ceramic for electrical insulation. The heater tracks are screen printed on top of the insulation. Finally a protective layer of enamel is applied, with exposed areas for electrical connections.
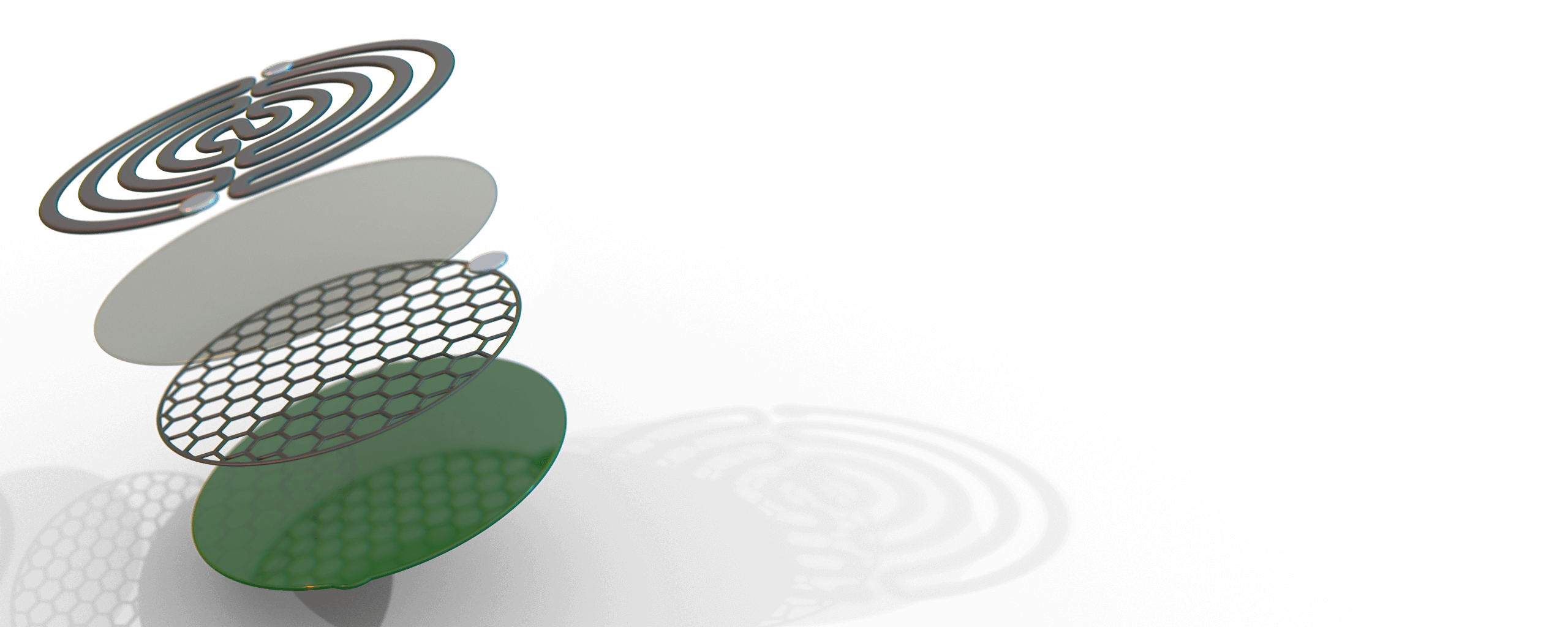
Element Substrate
The element substrate is the carrier for the enamel and the screen printed layers. Typically the substrate is stainless steel, however other materials such as ceramic can also be used. The substrate can be virtually any two dimensional shape. Three dimensional forms which can be screen printed, such as tubes, are possible.
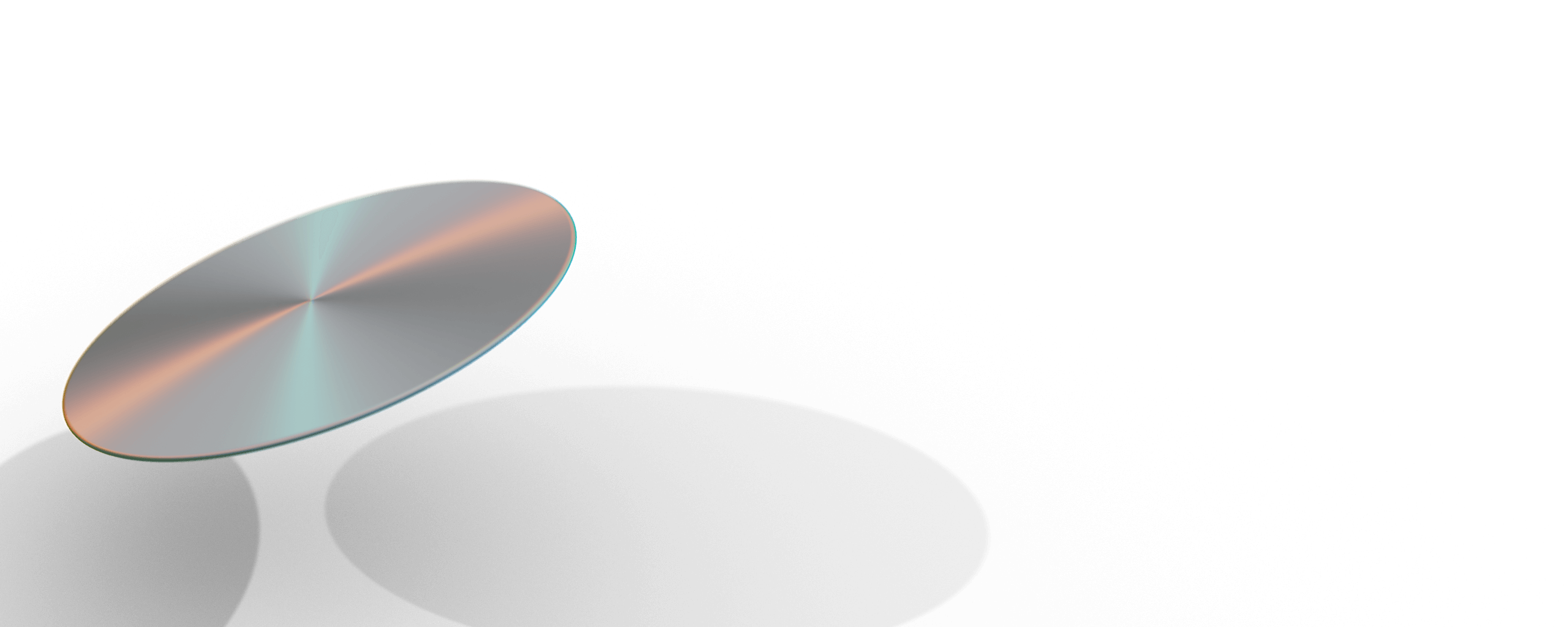
Insulating Enamel
The enamel layer electrically insulates the substrate from the screen printed heating tracks. This is unique to Ferro Techniek and they can adapt the formula for different application requirements. eg 230V 3kW or flexibility or 800V DC.
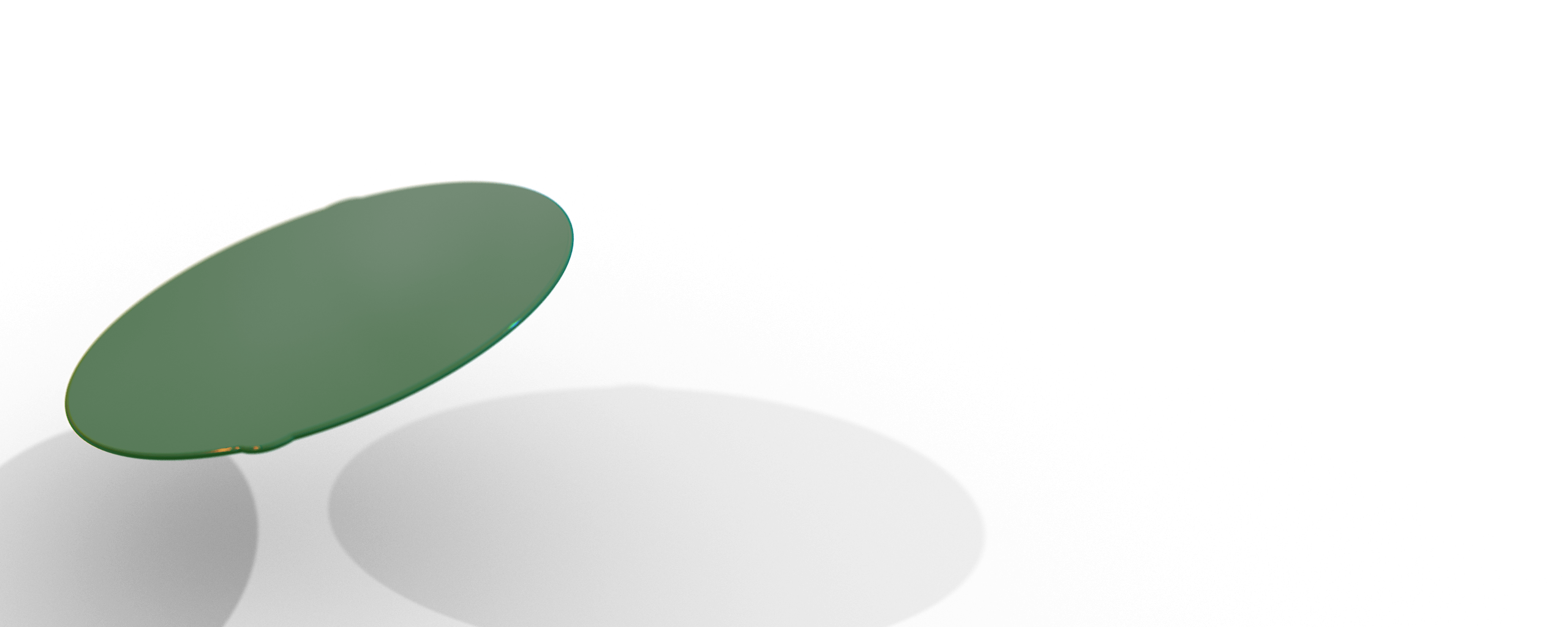
Thick Film Heating Tracks
Resistive tracks are screen printed and fired onto the dielectric, to provide the heating function. By varying the chemical composition and the geometry of the tracks, the element power and heat distribution can be finely controlled. Silver is selectively printed to create cooler, lower resistance areas for making electrical connections. For information on more advanced track design, see the link below.
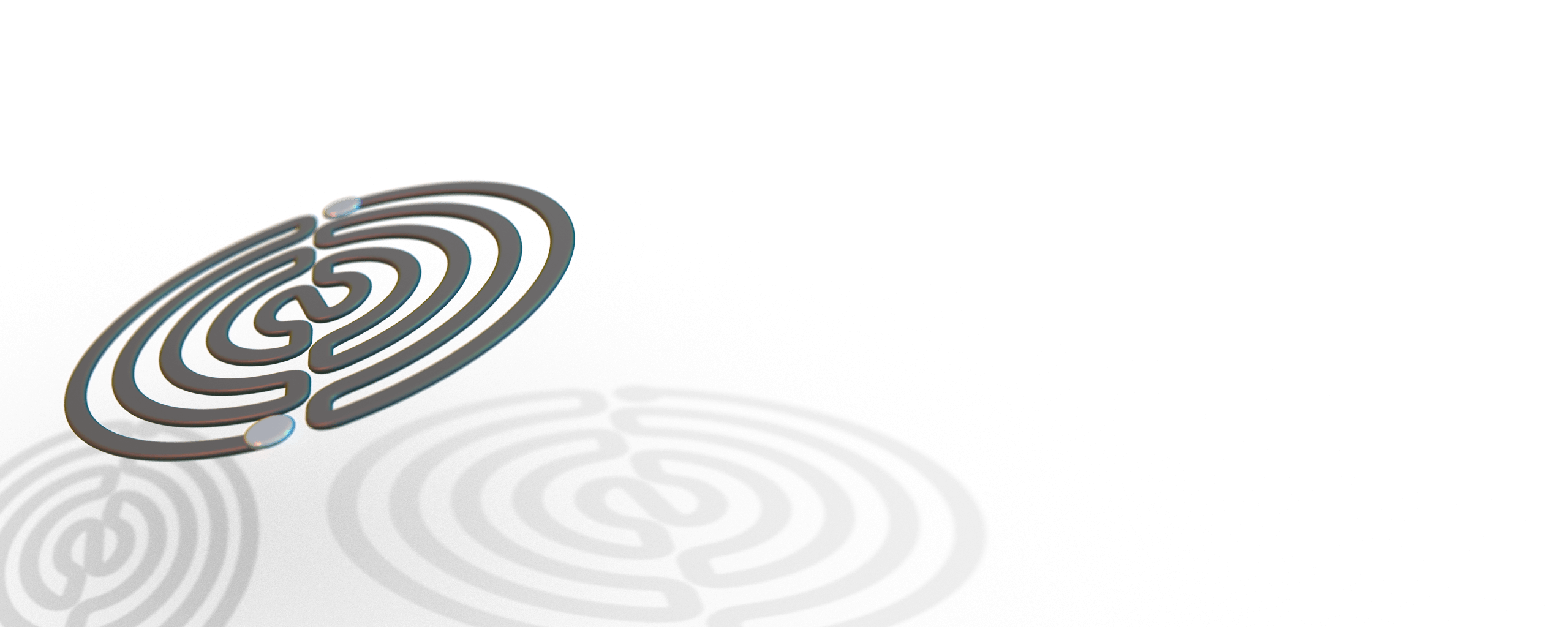
Element Cover Enamel
The element cover enamel is a protective coat over the heater tracks.
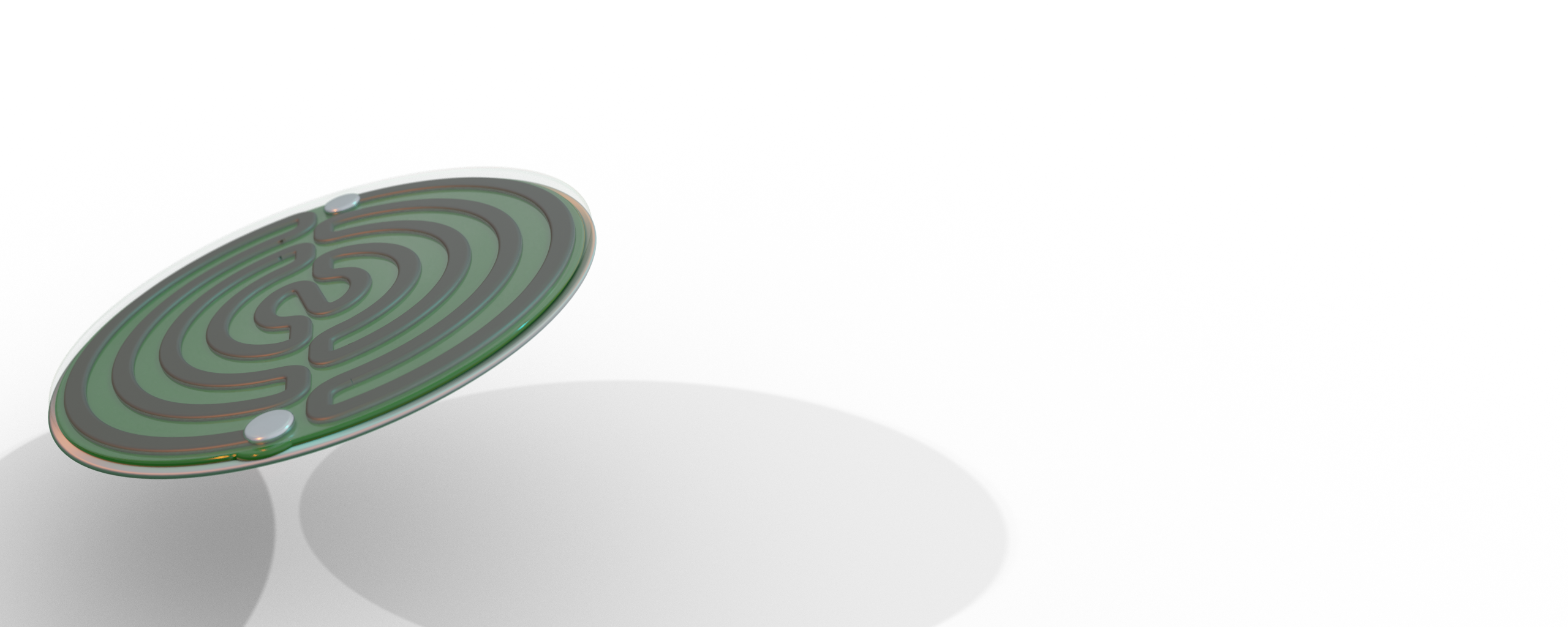
Track Layouts
Thick Film Track Layouts are often customised, to give even heat distribution across the thin substrate or to concentrate the heat where it is needed. A good example is in a milk frother to avoid burning. There can be multiple tracks for different purposes, such as fast heat up & keep warm or zonal heating.
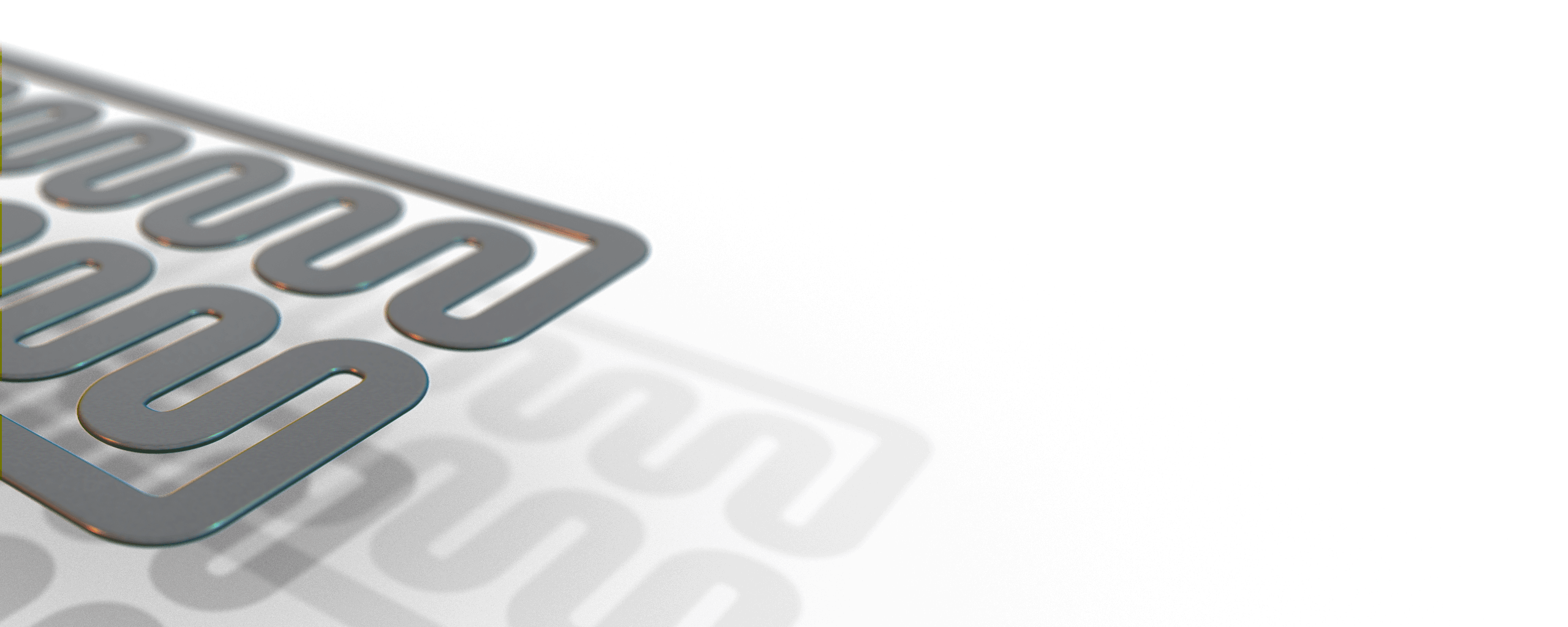
Track Gradients
The power density across the area of the heating element can be designed, to put more energy into some areas than others. This is useful when trying to optimise energy transfer from the heater into another material (eg food) as fast as possible, without burning it. To do this we can work with the track material, the width of a track, and the spacing of the tracks. Narrower tracks, close together = hotter
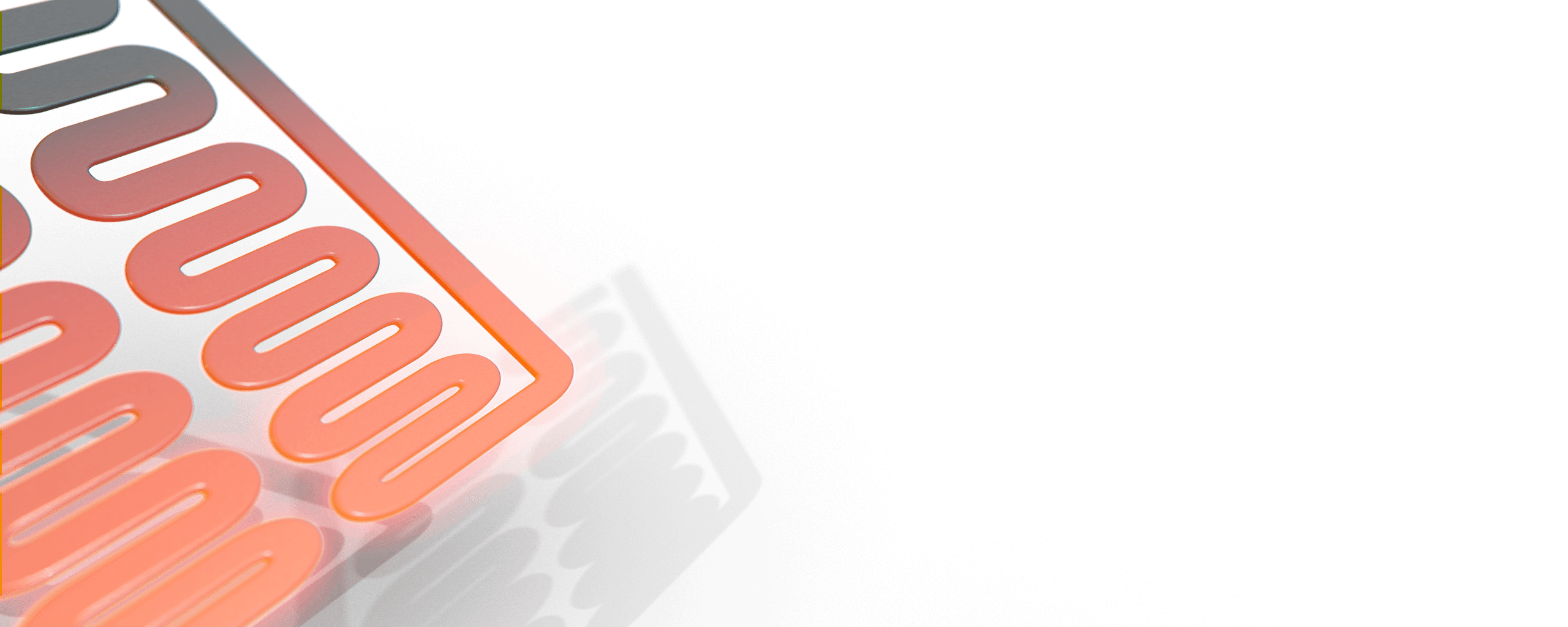
Track Zones
Separate heating zones can be applied to an element, with their own electrical connections and control.
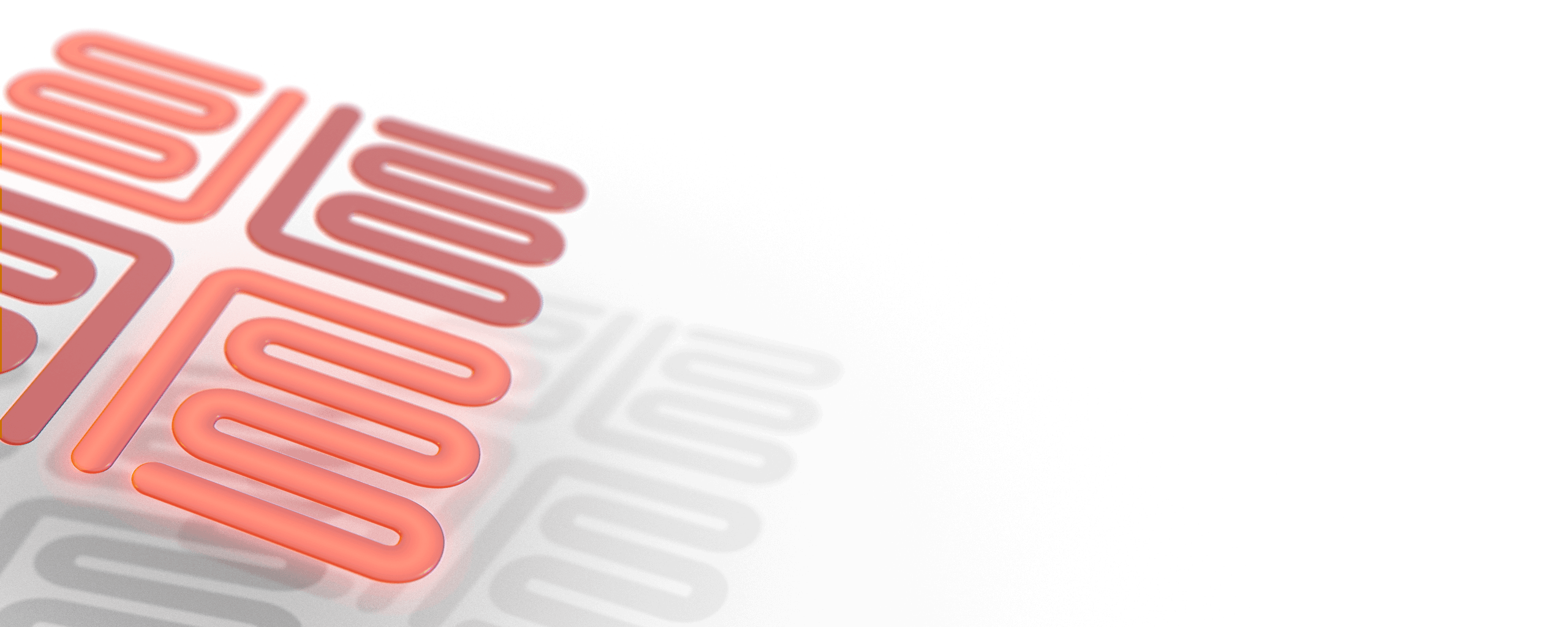
Dual Tracks
More than one track can be applied to the same surface area to offer multiple power levels. This can be used to give full power & accelerate the heater to temperature and then switch off a track, dropping down the power to hold it at temperature.
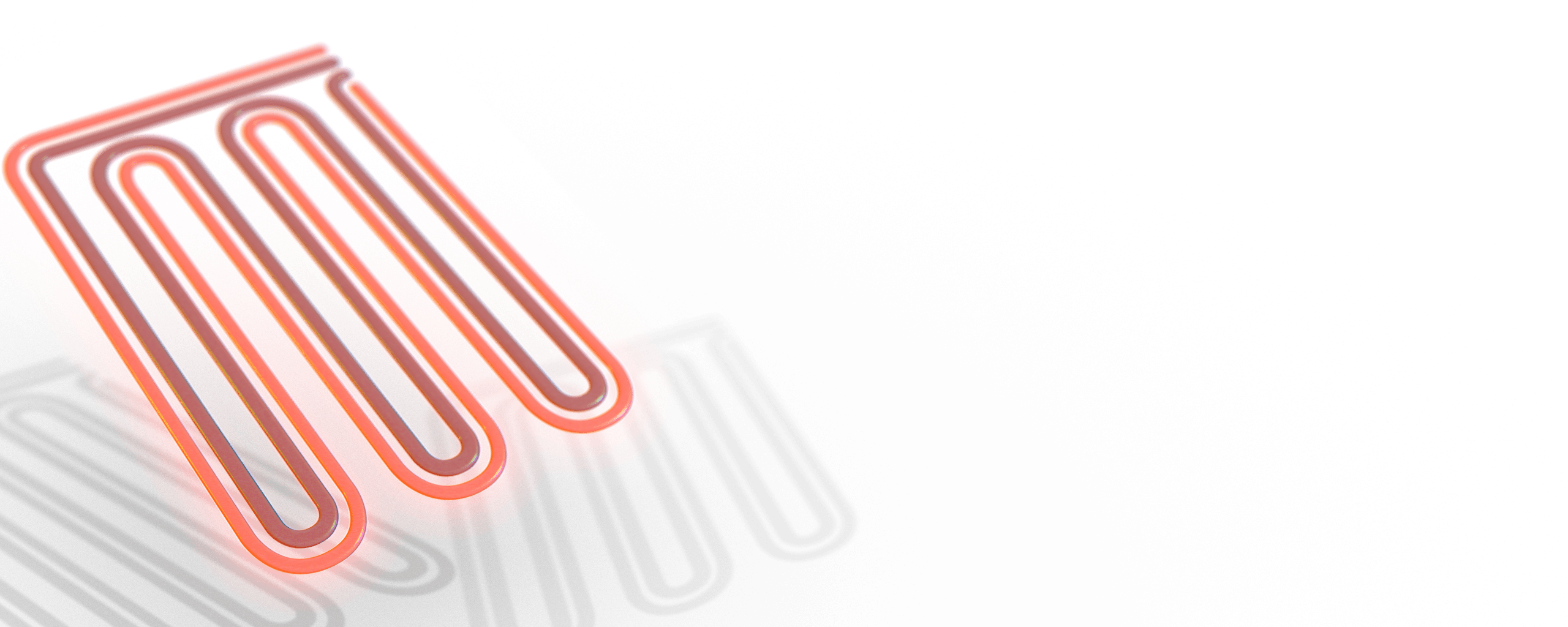
Sensor Tracks
Sensor tracks can be integrated. An example is an NTC track, to sense the temperature based on resistance.
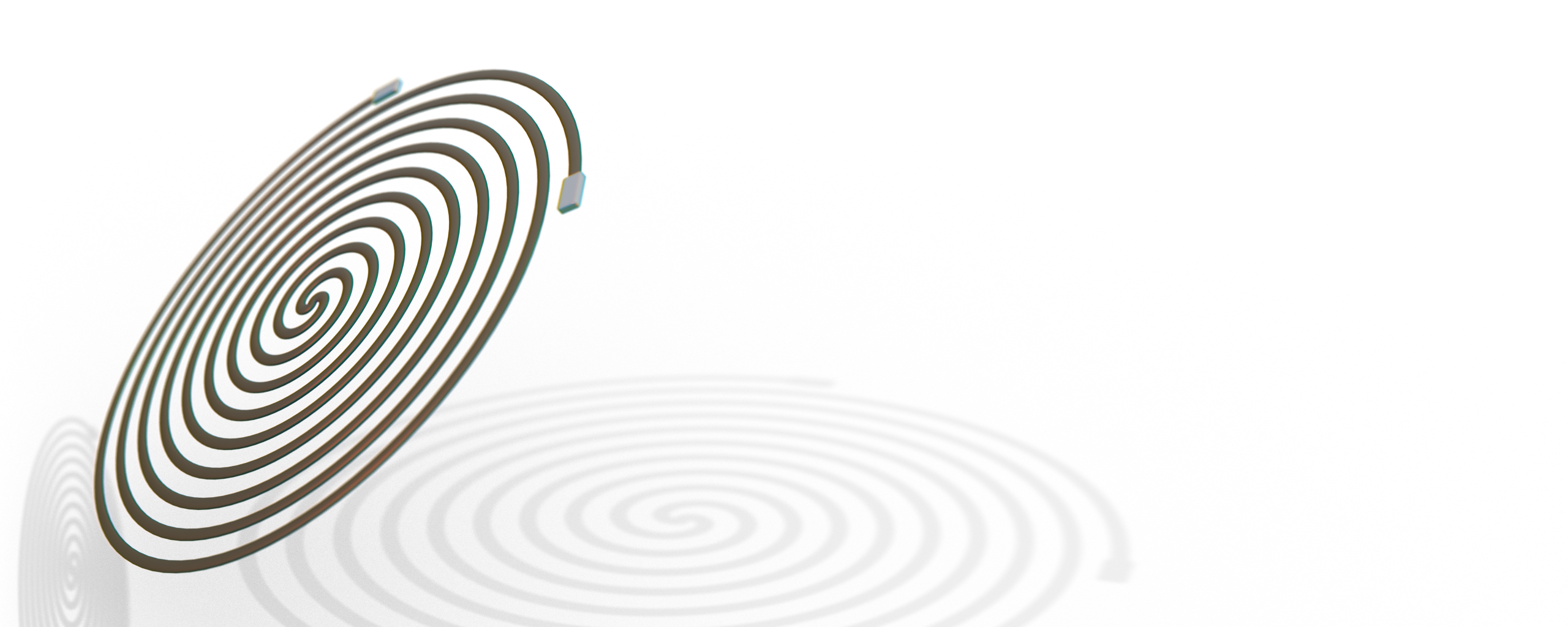
Substrates
The element substrate acts as the carrier for the enamel and screen printed layers. Typically the substrate is stainless steel, however other materials such as ceramic can be used. The substrate can be any two dimensional shape. Three dimensional forms, which can be screen printed, such as tubes, are possible.
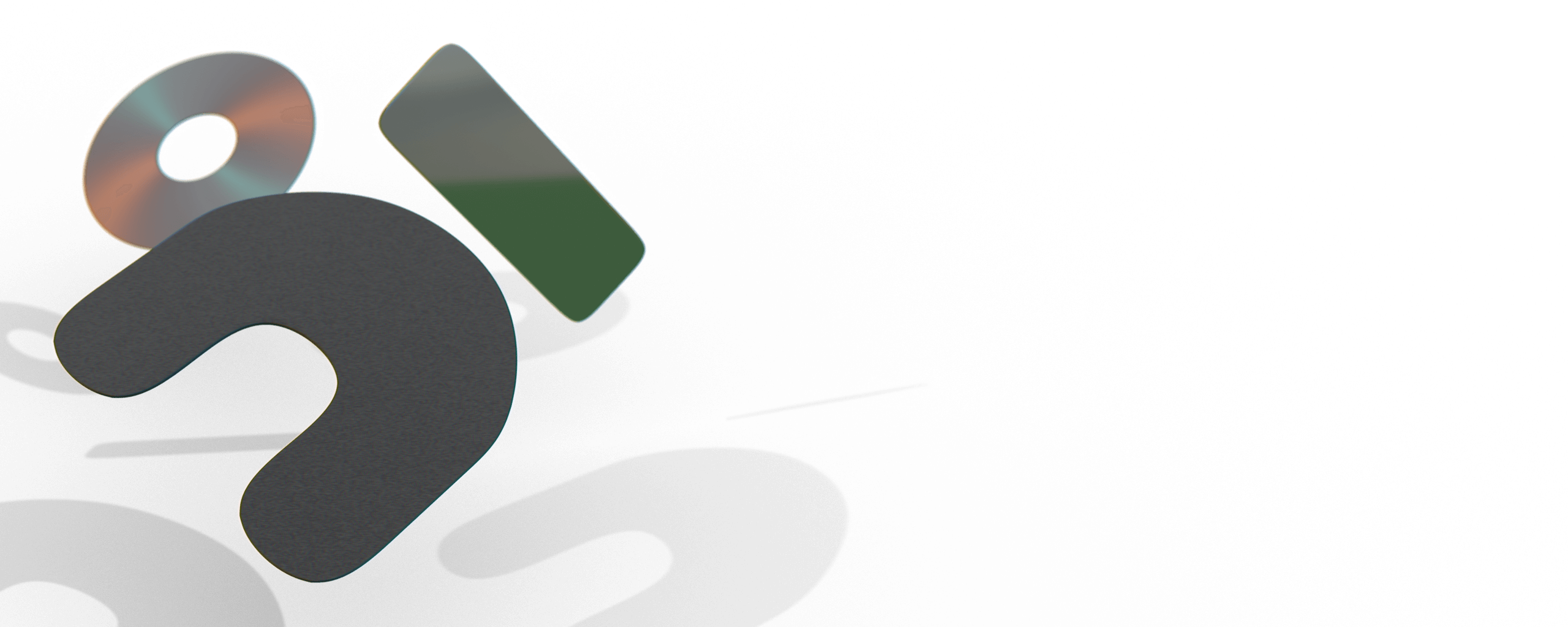
Materials
Stainless Steel is the most common substrate we use, however not the only one. We can use different metals & ceramics. Ultimately the substrate will be determined by the application requirements.
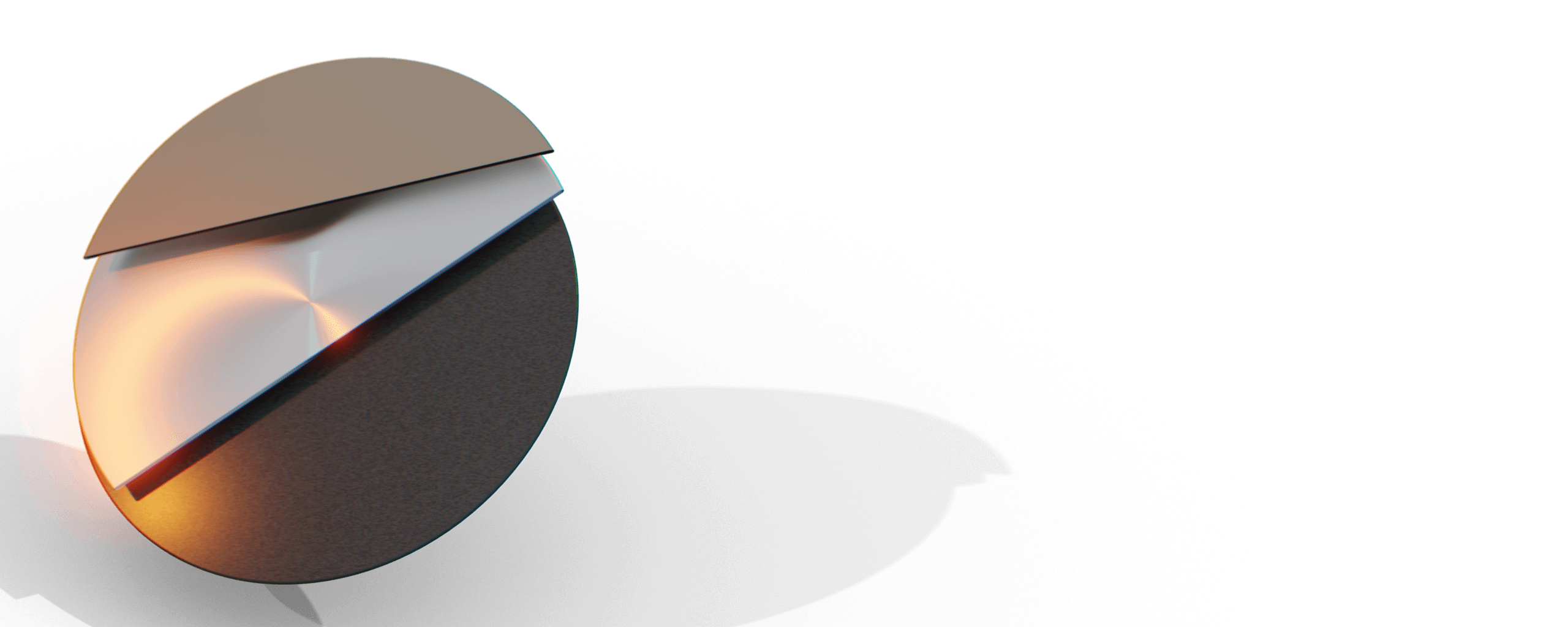
Planar Shapes
Applying the tracks is a precision screen printing process. This means the elements can be virtually any two dimensional shape. This includes holes through the substrate. One limitation is that its not too large to fit inside our furnaces for processing.
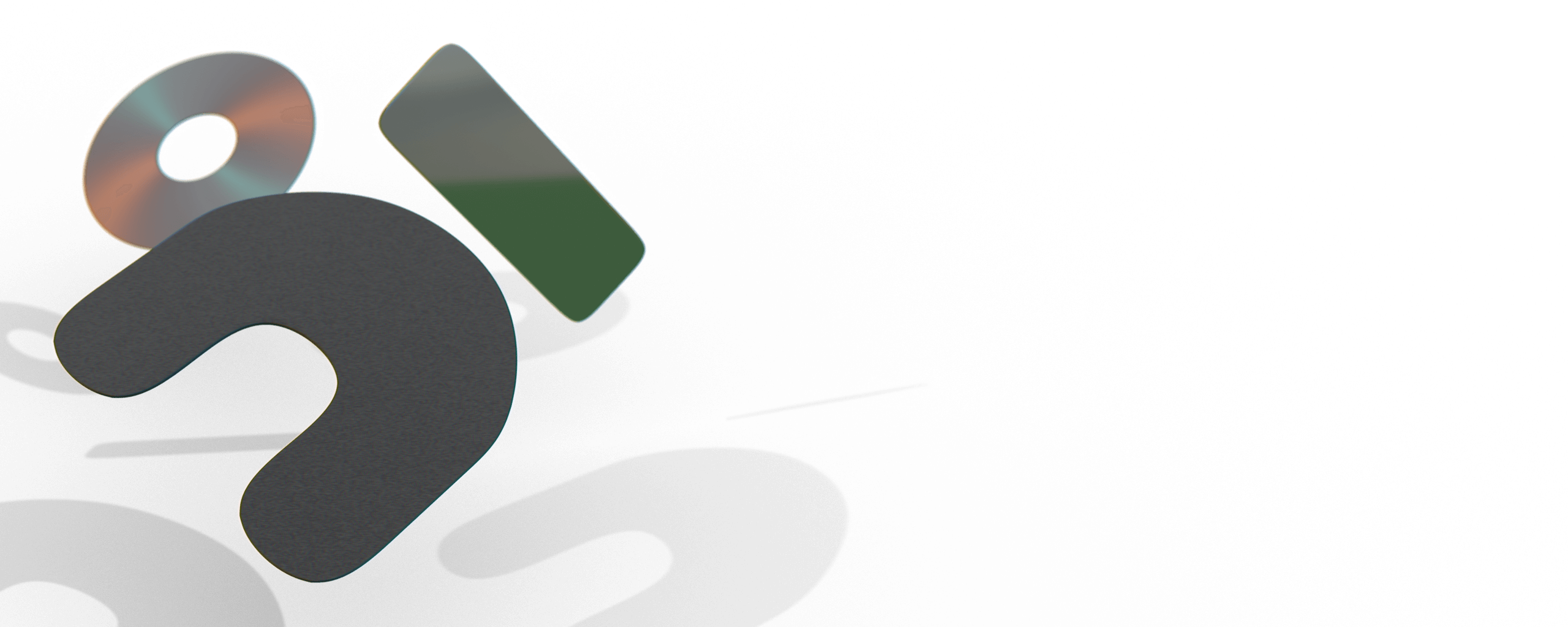
Assemblies
Thick Film Elements have extensive assembly options, and can even form an integral part of the structure of your product. Whether housed in a plastic moulding, welded into a metal vessel or directly brazed to the element substrate, there will be an option for your project.
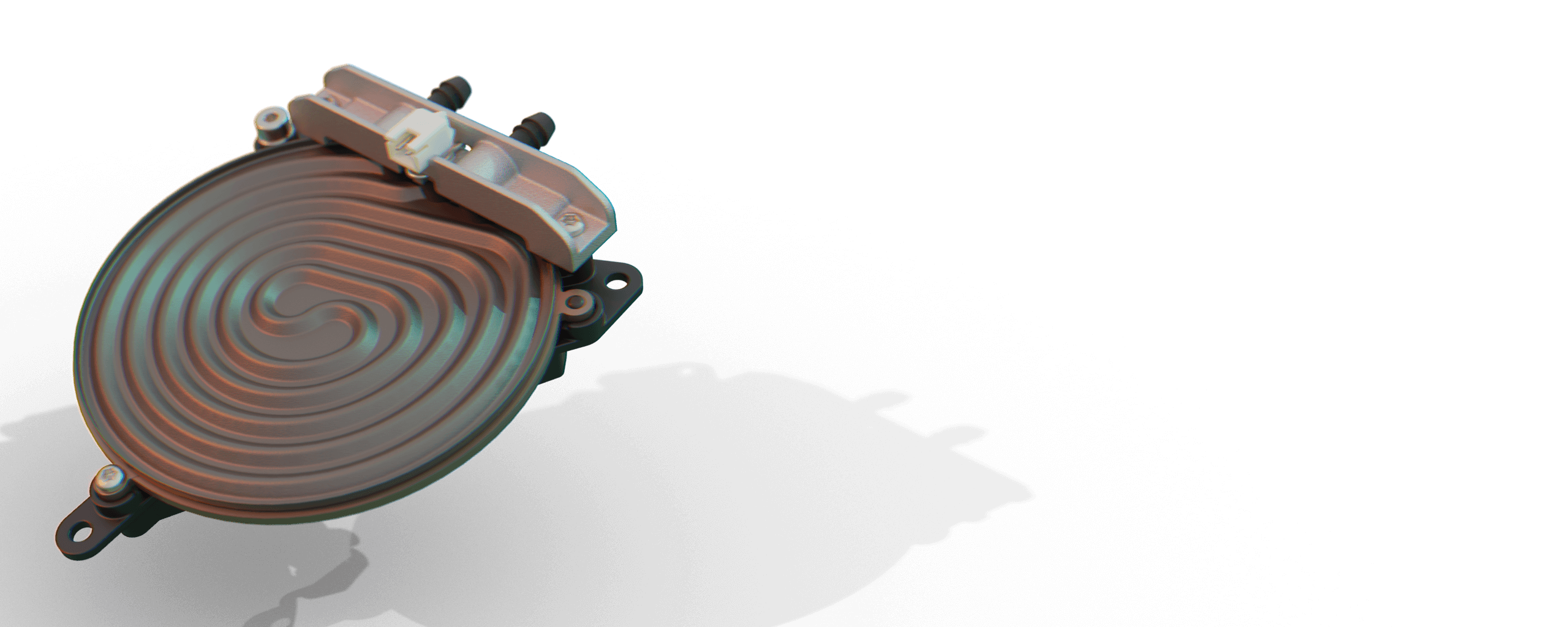
Brazed Assemblies
With a steel substrate, other assemblies can be brazed directly onto the element. The process is exceptionally durable and long lasting. We braze steel to steel in our Flow Through Heaters creating an assemble that can operate at extreme high pressure (20 bar). We can also braze steel to aluminium as seen in the Fin Pack for transferring the heat from the element into an air or gas stream.
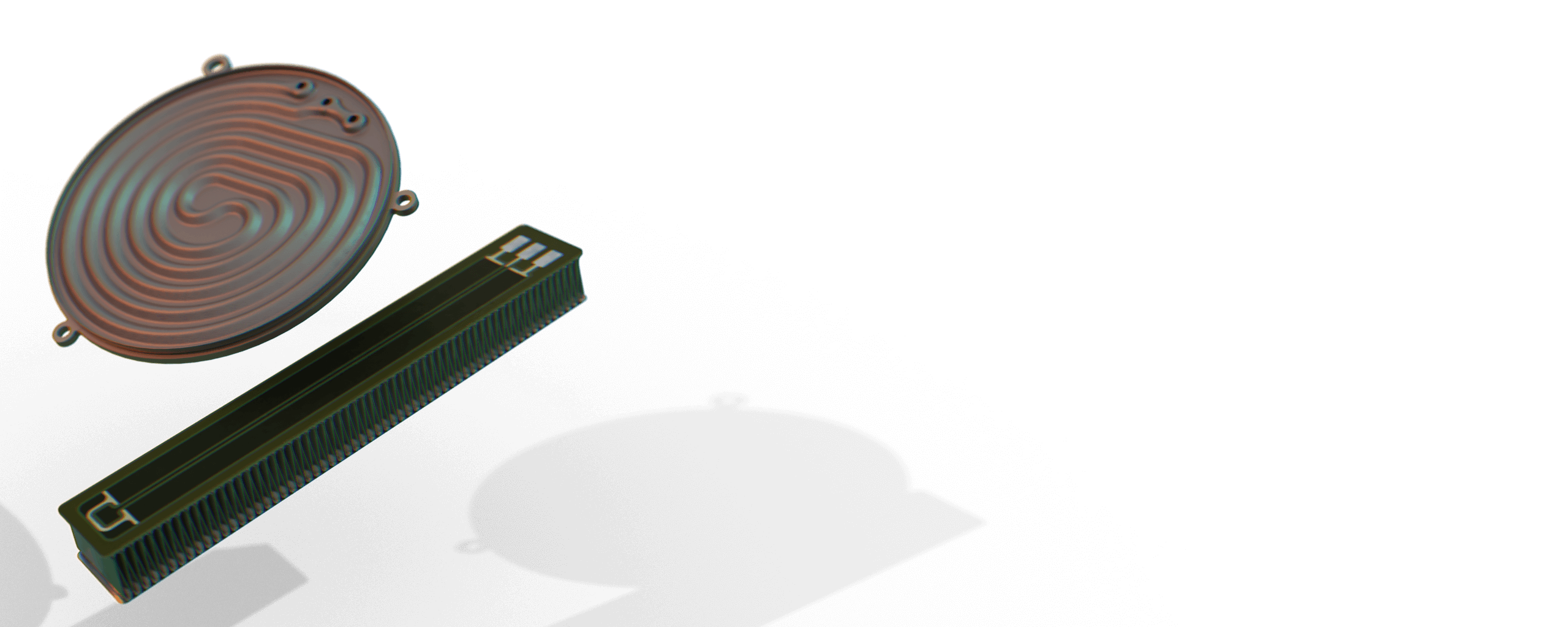
Laser Welding
Thick Film elements can be laser welded into larger assemblies, like bowls or other vessels.
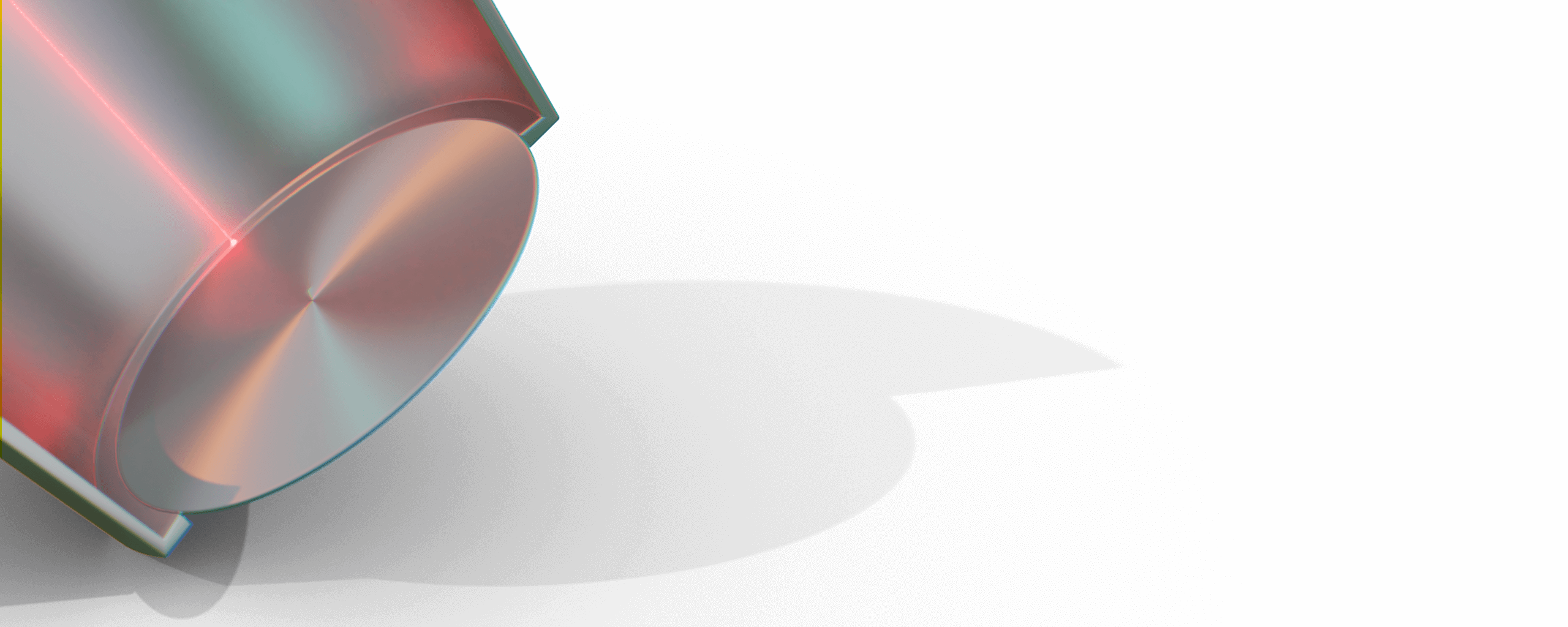
Compression Seals
A Thick Film element can be mounted in an application by using a compression seal. This is the technology most seen in kettle-like applications. In-particular Ferro developed a method using side compression (radial rather than axial) which has proven extremely reliable.
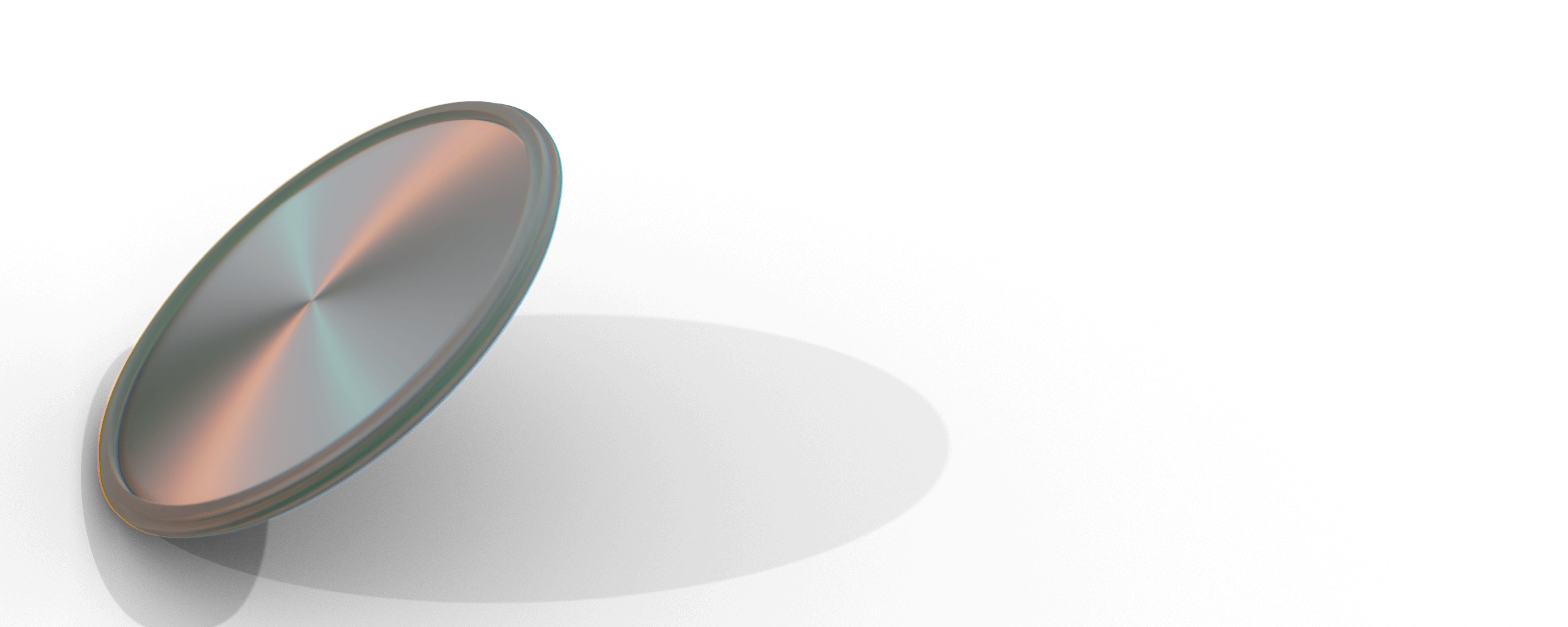
Kettle Controls
At Ferro Techniek we laser weld the kettle dry boil control & connector to the heating element. Our customers seal the assembly into their vessel, most often by using a compression seal. For more information on this application please speak to Otter Controls,
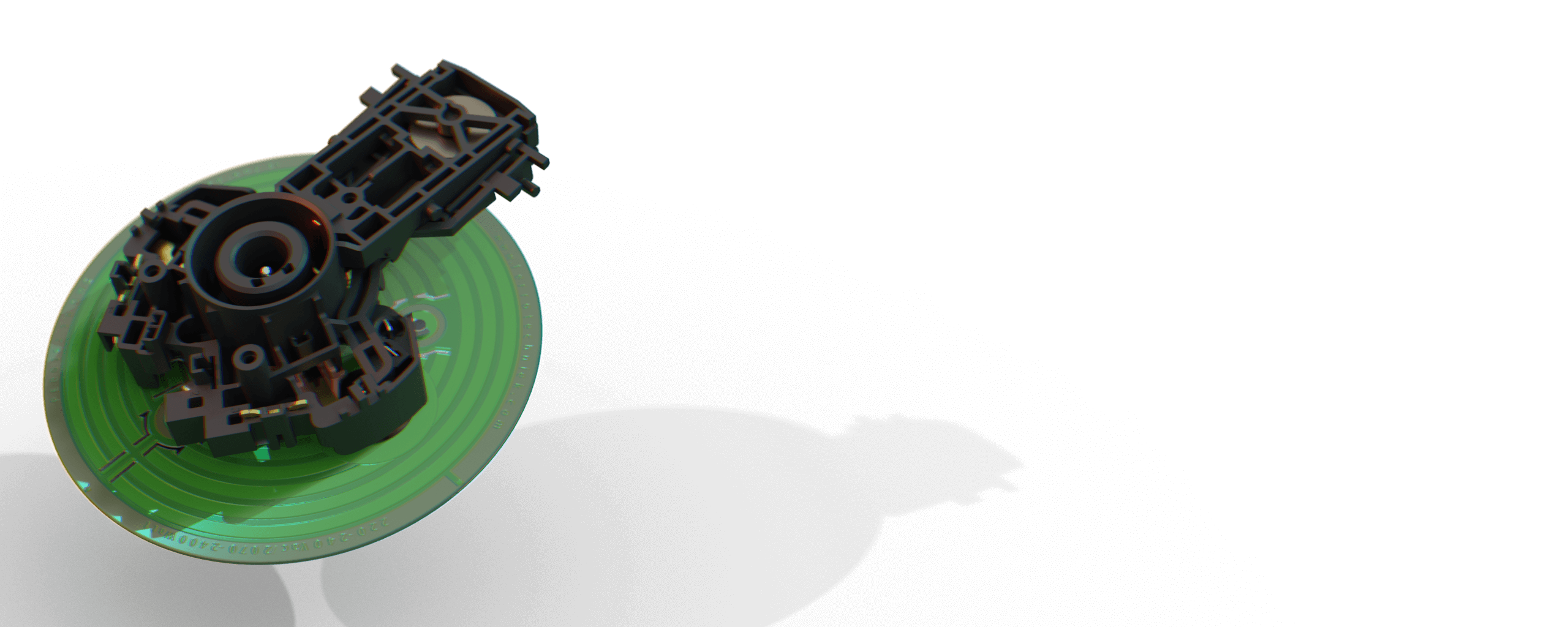
Custom Assemblies
As part of a larger group, we can manufacture a wider range of electromechanical assemblies using more varied construction methods via our sibling companies. See the Otter Controls website for what else the Group has to offer.
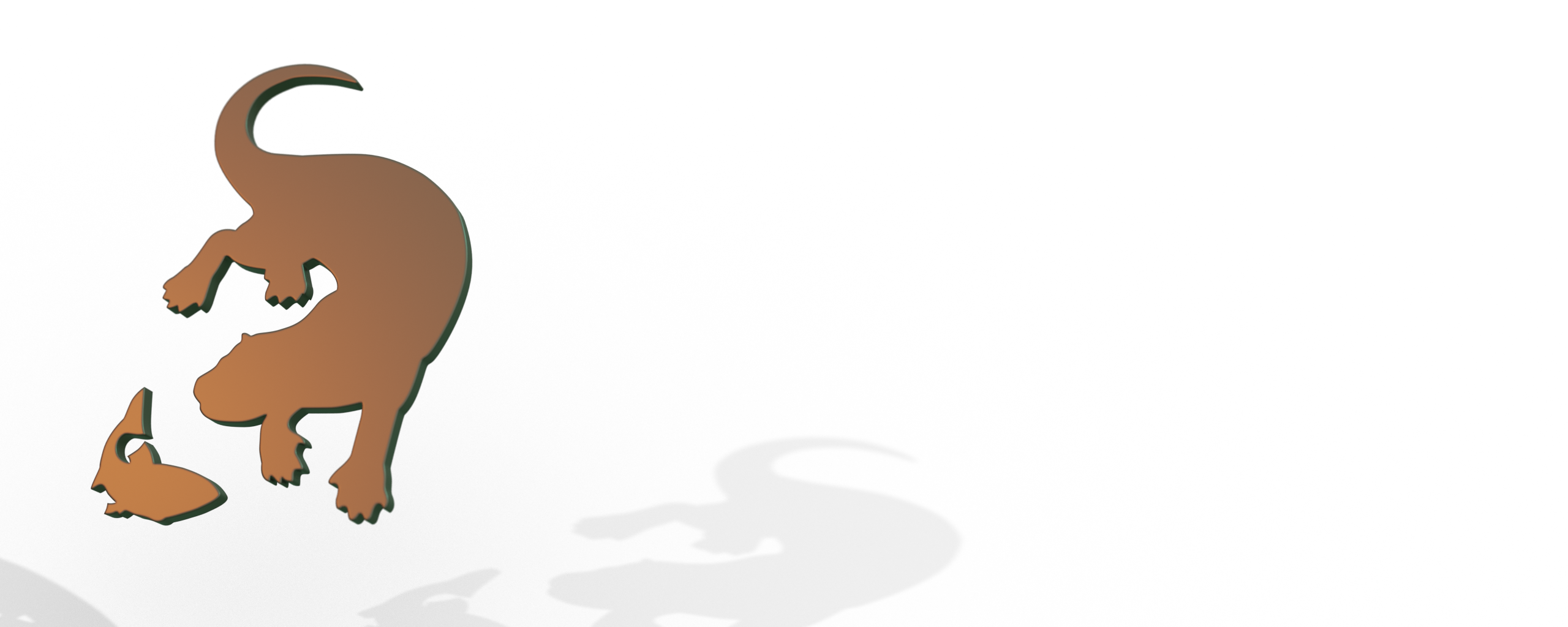
E-FAST and Integrated sensing
E-FAST – Electronic Full Area Sensor Technology, provides a means of near instantaneous overheat detection covering the entire element surface. When an area of the element exceeds a specified temperature, our specialised E-FAST enamel changes resistance. Electrical current is then allowed to leak from the heating tracks, through the E-FAST enamel to the detection grid. This leak is detected by corresponding electronics and appropriate actions taken.
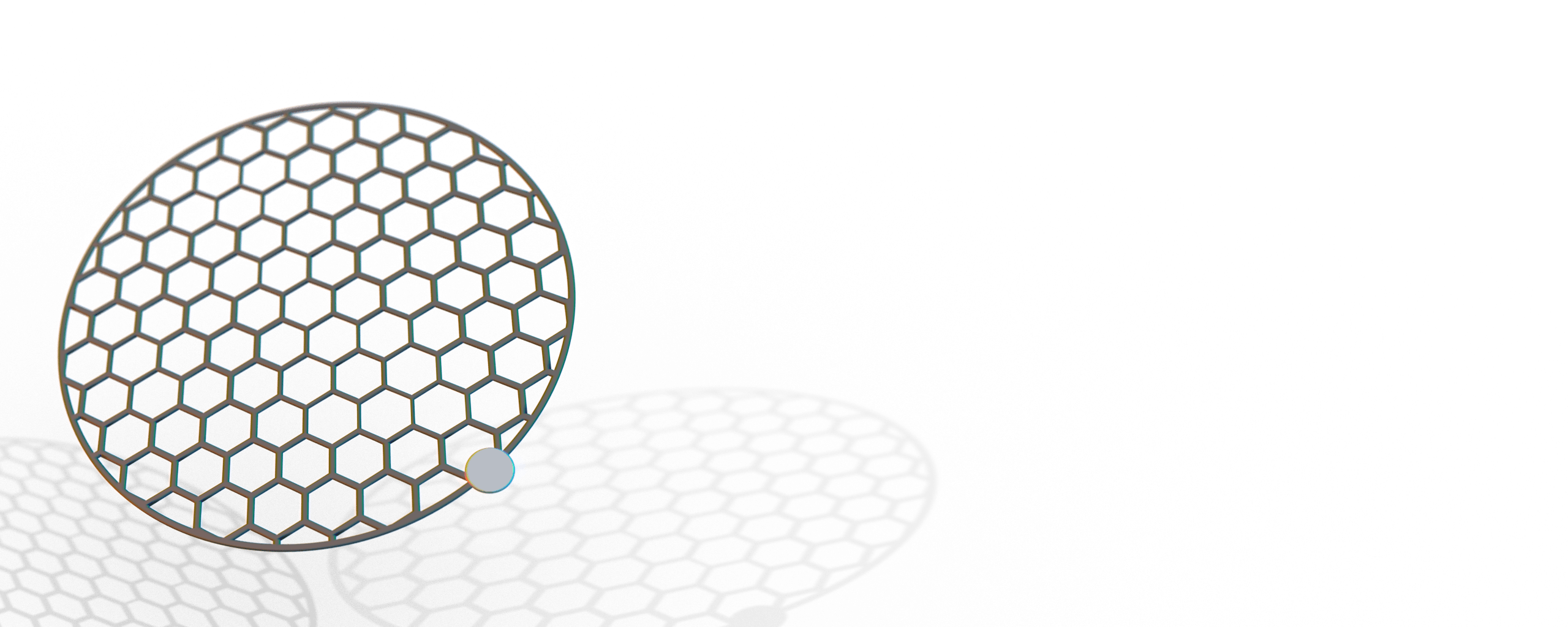
Embedded E-FAST
Embedded E-FAST uses vertically stacked layers. The heating tracks are separated from the detection grid by a layer of E-FAST enamel. When a section of track gets to a certain temperature, the E-FAST enamel drops in resistance and a leakage current passes through to the detection grid. This method instantly detects overheating as the E-FAST enamel is thin & in direct connection to the tracks & the grid. The element can have very high power density and be pushed to the limit without risk of a long switch off time & high overshoot shortening its life.
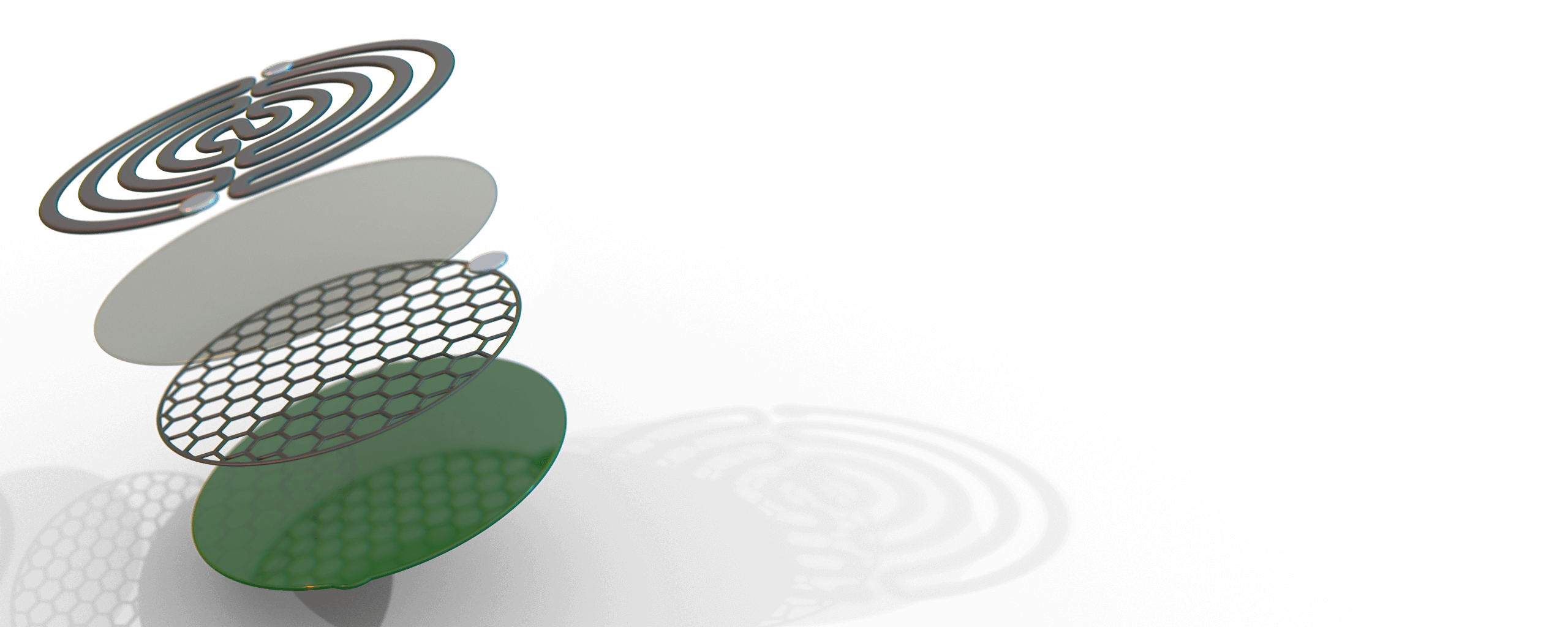
Parallel E-FAST
Parallel E-FAST relies upon the heating track and detection track being on the same layer, with the E-FAST enamel over the top and filling the gaps between the tracks. In this method when it gets too hot, the leakage current travels through the E-FAST enamel from the heater track to the sensor track, parallel to the element surface. This method is less layers than embedded E-FAST, so more cost effective.
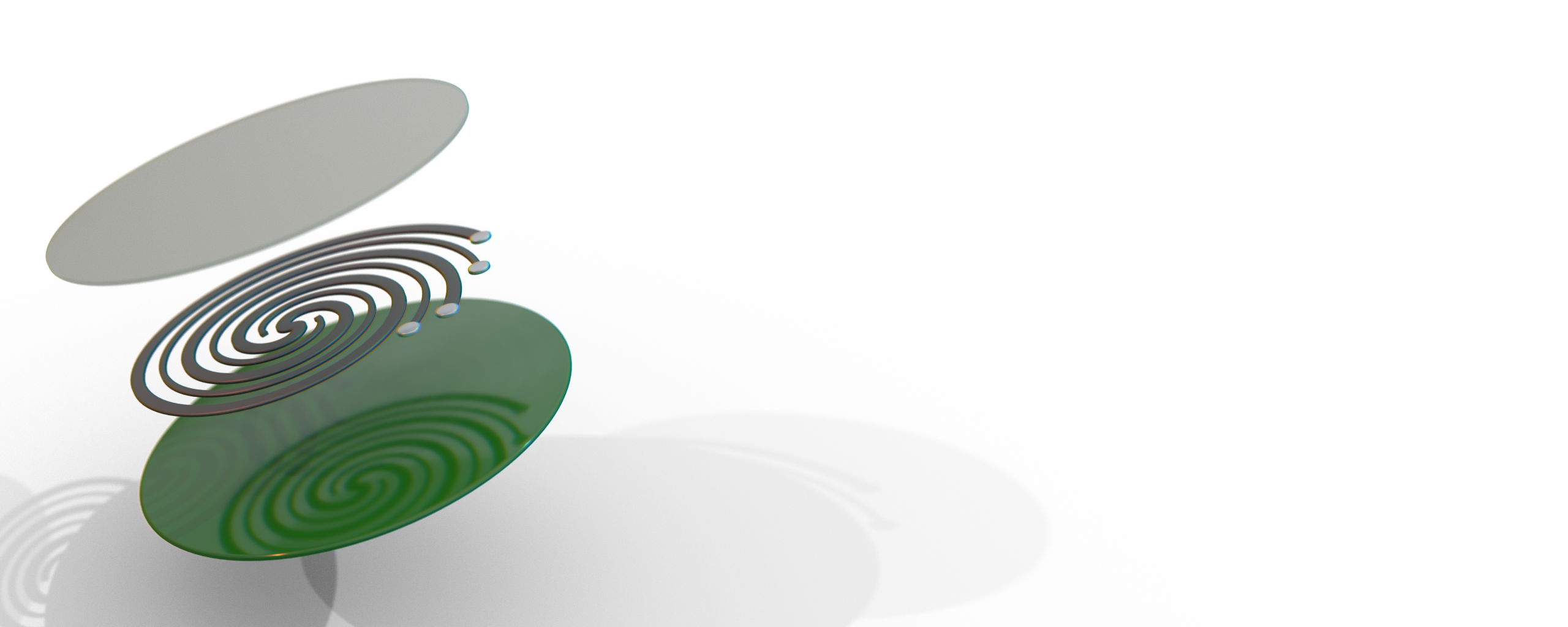
E-FAST and Steam
E-FAST can be used in more creative ways than a simple overheat detection method. It can detect food burning anywhere on the surface or lime scale build up. E-FAST is the underlying technology which allows our Flow Through Heaters to produce an instant, controlled flow of steam without causing overheating or self damage.
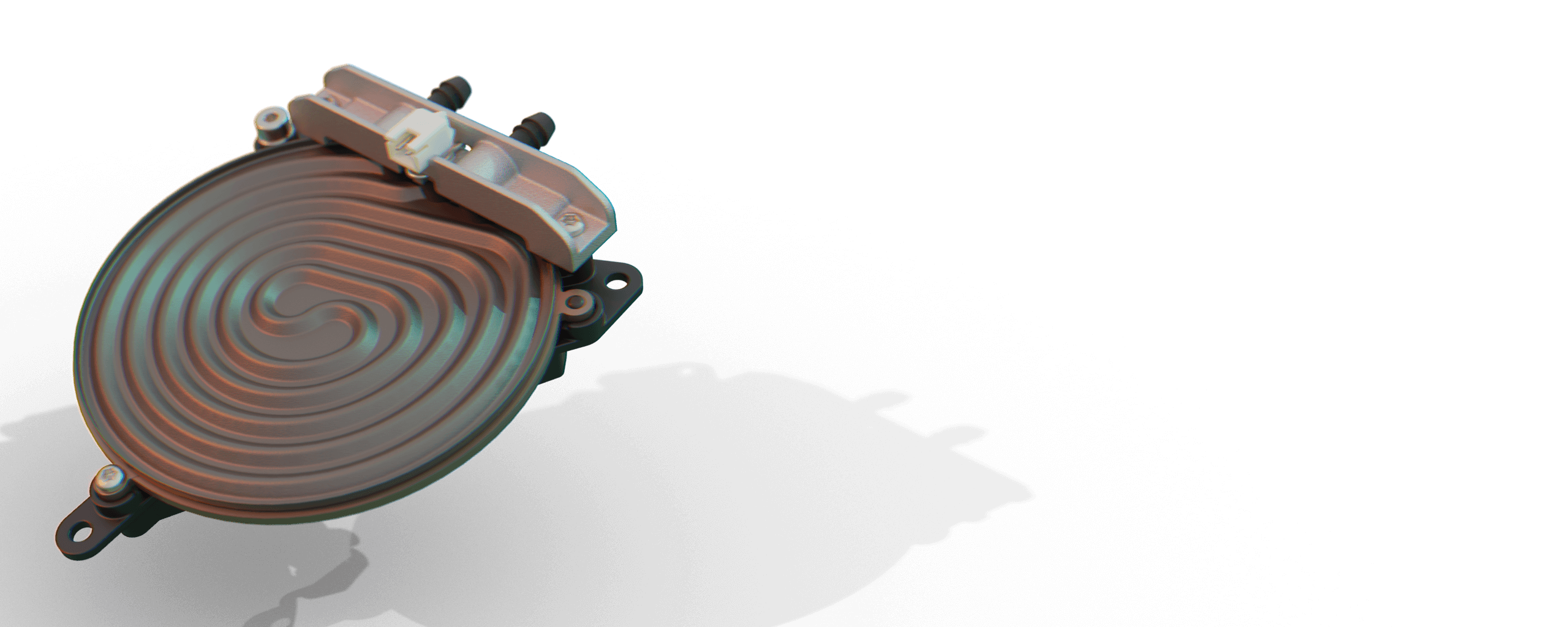
Protection and Connections
In addition to our E-FAST technology, more conventional methods of thermal protection are available. Thermal fuses and Bimetallic cut-outs can be provided and integrated into the element surface. We often find customers using these methods as a low cost secondary protection method to meet certification and approvals requirements.
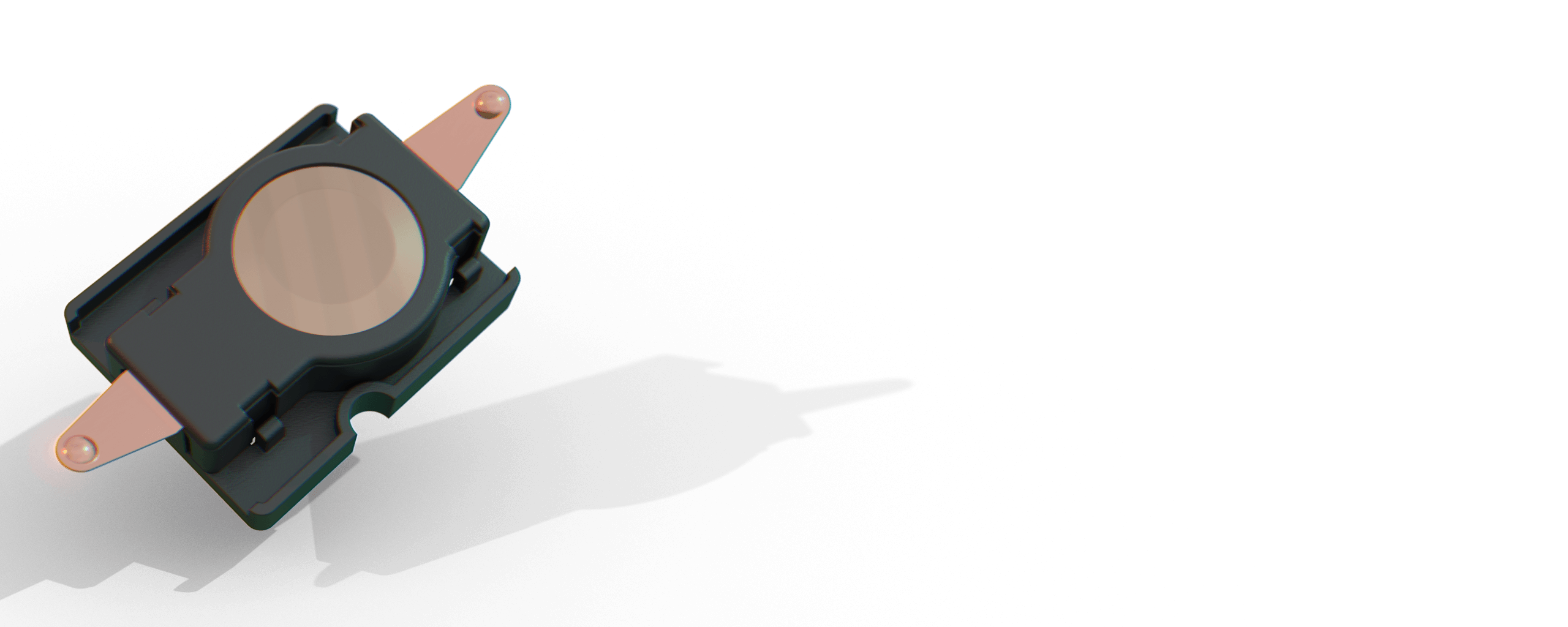
Electrical Connections
Ferro Techniek preference is spring connections to the heating element’s contact pads. There are a variety of methods and we are open to alternatives. We have vast experience to offer advice or Otter Controls can make you an assembly.
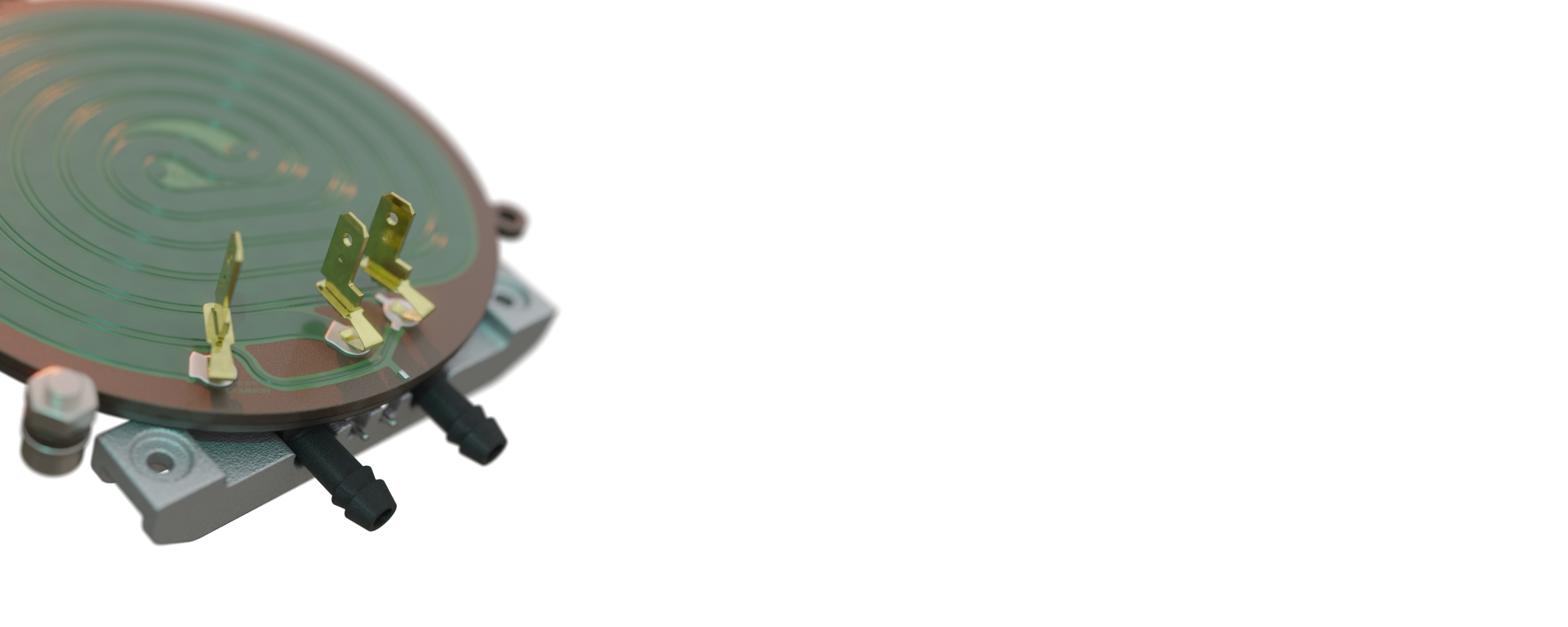